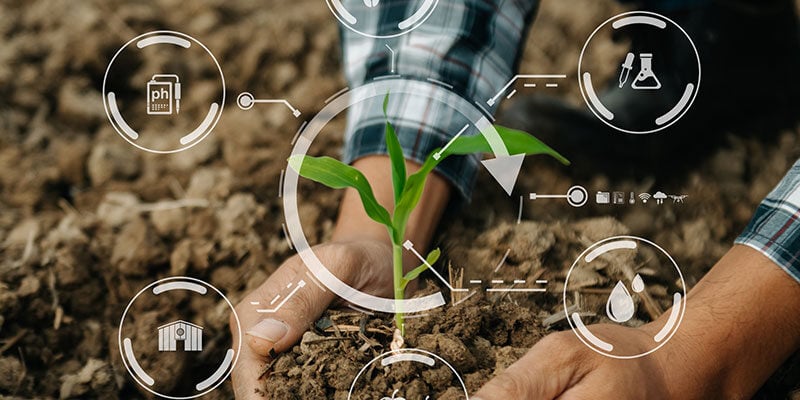
Listen to this blog
Smarter Strategies to Avoid Food Recalls with GS1
Harnessing Technology for Enhanced Food Safety and Reduced Recall Risks
In today's fast-paced food industry, the stakes are incredibly high for large-scale producers who must ensure the safety and quality of their products while meeting ever-tightening regulations. The challenge is formidable: ensuring that every item that reaches the consumer is free from contamination and defects. Advanced traceability addresses this challenge, reducing the risk of food recalls with GS1 and safeguarding public health.
Enter BL.INK’s GS1 Digital Link solution for the food production industry, a technology that transforms standard barcodes into gateways for rich product information and real-time data tracking. This technology can help food producers stay ahead of potential issues, enhancing transparency, and building consumer trust. With GS1 Digital Link, companies can provide detailed product histories, from origin to shelf, to meet and exceed global standards for food safety and traceability.
By adopting BL.INK’s solutions, companies can focus more on growth and innovation within a reliable, transparent supply chain, maintaining consumer trust and minimizing operational stress by avoiding food recalls with GS1.
Food Safety Revolution
Imagine this scenario: a large-scale producer detects a potential contamination in one batch of produce. Instead of the traditional, slower methods of tracing the issue, which could take days, the producer uses the GTIN-enabled 2D barcodes/QR codes to access real-time data to pinpoint the source of the problem. Within hours, they isolate the affected batch, preventing it from reaching consumers and avoiding a massive recall. This quick response saves the company from significant financial losses and protects the brand's reputation. This proactive approach helps avoid recalls and builds a foundation of continuous improvement and safety that consumers and regulators value highly.
BL.INK’s technology integrates seamlessly into existing systems, making it a practical addition to any large-scale food production operation. Companies can use this tool to track data to help meet and exceed the current standards for food safety and traceability. This commitment to excellence and transparency is what sets leading producers apart in a competitive market.
Enhanced Transparency
Dynamic product microsites are digital hubs linked directly to products through a QR code. When scanned, these codes lead to a wealth of detailed product information, from the farm of origin to the handling and safety measures taken before the product reaches the shelf. This level of transparency builds trust and strengthens a brand’s integrity and accountability, especially in scenarios involving potential recalls.
Let’s picture a scenario: A batch of apples has been flagged for potential pesticide contamination. With traditional methods, pinpointing and communicating this contamination could be slow and cumbersome, affecting consumer trust and potentially leading to a large-scale recall. With dynamic product microsites, however, the producer can quickly update the site with relevant information as the situation is resolved.
This immediate access to detailed, accurate information prevents crises and improves the everyday shopping experience for consumers. It empowers them to make informed decisions, knowing exactly where their food comes from and how it's been handled. For producers, it maintains a direct line of communication with the end consumer, even after the product has left the store, helping to avoid food recalls with GS1.
This approach takes proactive steps to ensure that each product holds up to the high standards consumers expect. In the event of a recall, these microsites allow for swift, targeted communication directly to the consumers affected, rather than a blanket broadcast that could cause unnecessary alarm.
Adopting dynamic product microsites enhances traceability and redefines it. It directly connects consumers and producers in a way that was previously not possible. These tools keep producers ahead of potential food recalls and sets a new standard in consumer engagement and trust, ensuring that food safety is never compromised.
Compliance Empowerment
Cultivating a compliance-focused culture helps food producers keep their operations sustainable and successful in today's market. As we navigate the complexities of food safety, embracing continuous improvement and rigorous compliance standards becomes a pillar for any forward-thinking company aiming to minimize food recalls with GS1.
BL.INK’s GS1 Digital Link solution creates a single source where all data about suppliers, batches, expiry dates, allergens and more can be accessed by consumers or producers, and anyone between. This solution helps embed compliance into the DNA of daily operations, ensuring every team member, from the floor worker to the executive, is aligned with the highest standards of food safety.
It’s vital to train staff regularly on the latest safety protocols and leverage real-time data to track compliance. Integrating compliance into daily operations is an opportunity for continuous learning and improvement. It’s about creating an environment where safety and quality are everyone’s responsibility. By making compliance a core part of the operational strategy, companies can turn potential challenges into opportunities for growth and innovation.
BL.INK’s GS1 Digital Link solution for food production supports this mission by providing the data and information necessary to implement these practices effectively by syncing all the data into a single microsite via an identifying QR code. The technology enhances traceability, which is crucial for compliance and for gaining insights into operational efficiencies and consumer preferences. These features lead to better decision-making and a stronger, more resilient business.
Building a culture of compliance and continuous improvement is crucial for any large-scale food producer committed to maintaining high standards of safety and quality. With the support of BL.INK’s GS1 Digital Link, food production companies can achieve these goals more effectively, ensuring a safer future for their products and their consumers, and avoiding food recalls with GS1.
Learn more about BL.INK's digital product passports.